The industrial environments can be extreme and challenging making the process control measures insufficient to minimise the risk. Therefore, using Personal Protective Equipment (PPE) is a must for anyone who is working in such areas. In the previous part of this blog series, we have examined the real world challenges that the safety professionals have to overcome to improve the compliance and reduce the risks without compromising the productivity. These goals often appear to be contradictory and can be very challenging to implement for the decision makers.
Luckily, the key to get around this issue is easily available in the safety standards for eye protection. Before we jump to the solution to the problem at hand let’s look at the evolution of safety eyewear.
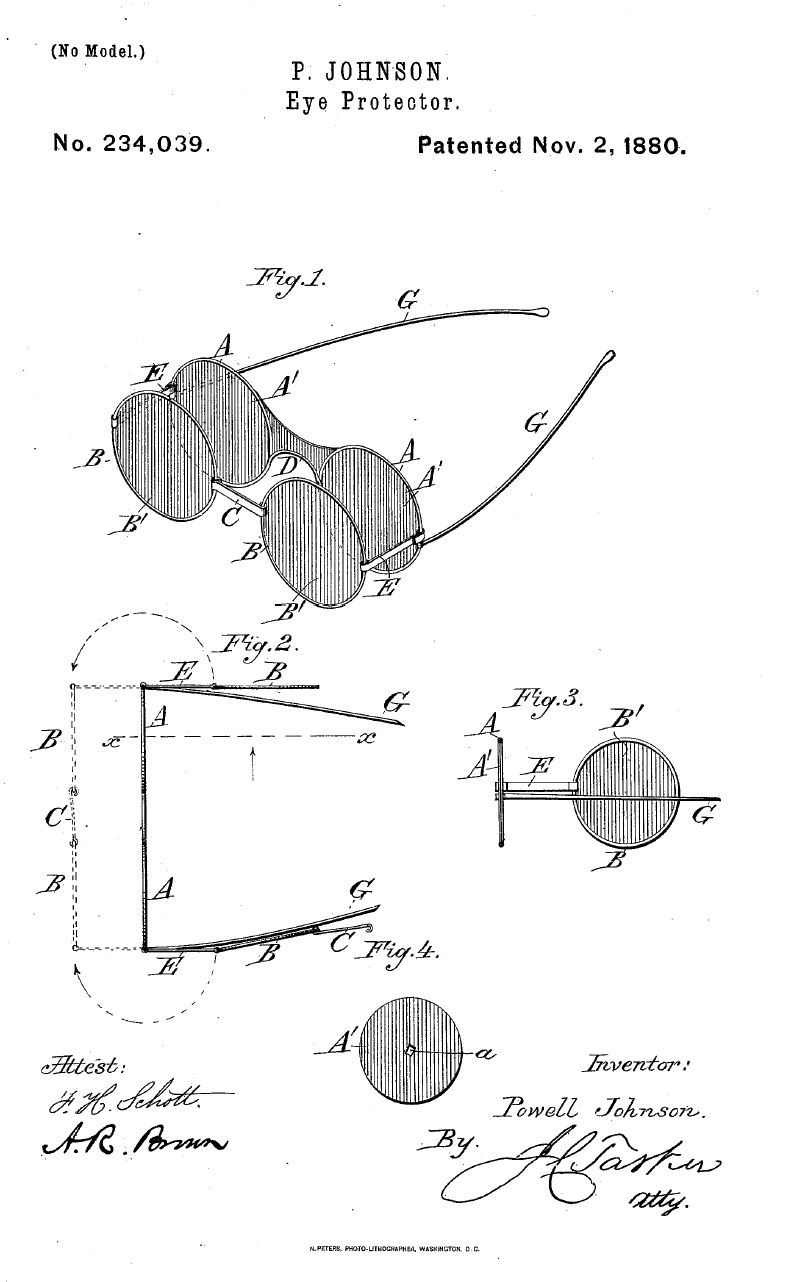
The earliest references of using an eye protection for industrial applications dates back to 1880 when an African-American inventor, Powell Johnson, secured a patent for ‘Eye Protector’1 that he designed to minimise glare by placing two circular screens in front of each other. These screens were made of, believe it or not a semi-opaque fabric! While it was an interesting invention to reduce the glare while working in front of furnaces it obviously lacked the impact strength needed to prevent eye injuries from flying particles.
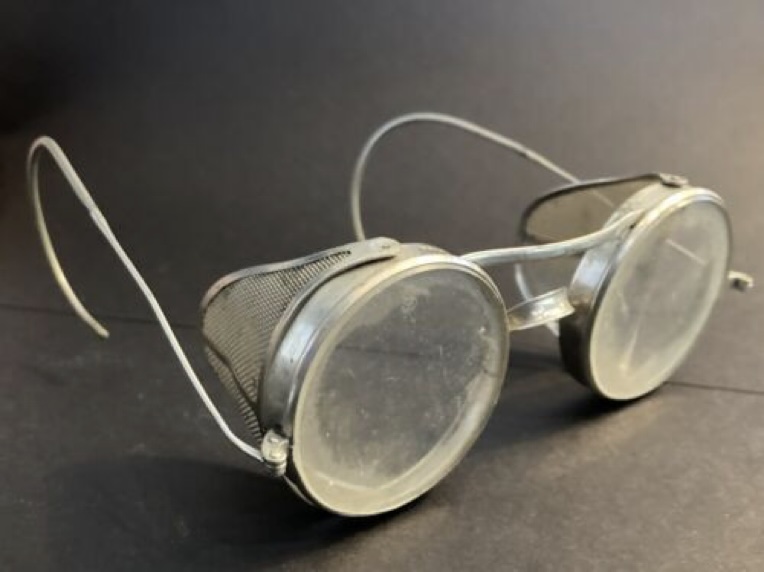
The importance of protecting eyes from non-glare hazards, like mechanical projectiles, was recognised in early 1900s. The ‘Julius King Optical Company’ in the United States developed the first safety goggle called SHANIGLAS in collaboration with ‘American Optical’ in 1909. Following that in 1910 Garrett Morgan gained a patent to include safety glass in his gas mask and the protective eyewear as we know today came into being. His invention became popular during the First World War and later evolved to be used as car windshields.
These first generation safety eyewear designs were bulky and uncomfortable for most part of twentieth century as they were made from metals, leather and toughed mineral glass and hard resins. These materials were brittle and presented a secondary hazard to the eyes and face when used for eye protection. In early 1970s Gentex Corporation (manufacturer of tactical helmets) revolutionised the safety eyewear by manufacturing an optical lens made out of polycarbonate for the first time. Polycarbonate being a strong material offered far superior impact protection than toughened glass and it remains the material of choice for safety eyewear even to this date.
While the design of safety eyewear was getting upgraded, the ANSI standard for eye protection remained undefined till 1968 and in the initial days covered only the construction industry. Real attention was given after OSHA was established in 1971 and referred to the 1968 version of ANSI standard for eye protector as a rule. The ANSI Standard Z87.1 has undergone a few updates since then and the latest version is from 2020.
The Indian version of first safety eyewear standard IS 59832 was published in 1971 by the Bureau of Indian Standards (BIS) under the name ‘Specifications for protective filters for welding, cutting and similar applications’. The scope of IS 5983 was expanded in 1980 to cover hazards like small particles flying at high velocity, molten metal, chemical splashes, dust, gases, optical radiations (ultra-violet, infra-red and glare from intense visible light) pose hazards which are likely to impair vision or damage the eye and the standard was renamed as ‘Specification for Eye Protectors’.
The standard at that point had recognised both toughened glass and plastic as lens material but for several years the safety eyewear was made using toughened glass as lens material. Even today some safety goggle tenders from public sector companies specify toughened glass as lens material. What is interesting to know that even in 1980s the standard was quite evolved. It had touched upon aspects of wearer comfort, fitment, ventilation etc and there was a corollary standard for the testing methods (IS 7524:19803). This version of the standard recognised two separate product categories – eyewear with optical protection only and eyewear offering protection from mechanical impact. The standard also identified special purpose products offering protection from - high velocity particles or molten metal and hot solids or chemical splashes or dusts or vapours and gases, and it included a product marking guideline to map a product for application. The IS 5983 was recently withdrawn and a new standard IS 8521 (Part 1) was introduced in 2021. This standard is mirrored and harmonised with ISO 16321. The standard for test methods have been also updated as IS 7524 (part 1 - part 4) and they mirror ISO 18526 (part 1 – part 4).
One might think that the safety standards would primarily focus on product design and testing and they are of little help to users or decision makers. Thankfully that’s not true. Most safety standards include a mandatory product marking guideline that provides the crucial information, to the decision makers and users, to select an appropriate product offering the desired protection from the identified hazard. In the next part of this blog series we will explore the product marking in greater detail and finally understand how this knowledge helps to over product selection dilemma and improved compliance.
References
1 https://patentimages.storage.googleapis.com/a7/bd/b8/b78300a62f59a8/US234039.pdf
2 https://law.resource.org/pub/in/bis/S02/is.5983.1980.pdf
3 https://law.resource.org/pub/in/bis/S02/is.7524.1.1980.pdf