In this concluding part of our Safety Eyewear blog series, I will explain how awareness of safety standards can enhance compliance and lead to better protection in the workplace
In complex industrial environments, a ‘one-size-fits-all’ approach to PPE isn’t effective. Recognizing this, safety standards have long acknowledged the need for specific solutions. Almost all standards for Safety Eyewear require the manufacturers to put the product through a series of tests that assess the ability of the product to address the typical workplace hazards. These hazards can generally be categorized into optical hazards, impact from flying objects, liquid splash, and fine particles. Safety standards outline specific test protocols to evaluate a product’s performance against each of these risks. This means the products which are certified have gone through the defined tests and should typically help the users to address all challenges at their workplace and then ‘one product fits all’ approach should have worked but in reality, the standards recognizes that all users may not face all the hazards simultaneously and overprotection can only increase product costs and implementation challenges.
With that thought in mind, the standards have defined some mandatory compliance parameters ensuring general or base level protection and have separately recognized optional/additional compliances to confirm suitability of the eyewear for specific and uncommon hazards. However, the standards go one step further by mandating the manufacturers to include permanent markings on the product (both on lens and on the frame) which allow the user to differentiate between products offering bare minimum compliance from those offering special hazard specific compliance.
The knowledge of the product markings will empower the users or safety professionals to choose the right product for right application there by increasing the compliance.
Lets understand the product marking requirements of ISO and European standards
MANDATORY MARKINGS
Optical Clarity
If we have to wear a product in front of our eyes our basic expectation would be that the product should allow us to see clearly. Thus, ‘Optical Clarity’ is the first mandatory test defined by all standards for safety eyewear requiring the lens to allow luminous transmittance of not less than 74.4% and have a Spherical and Cylindrical powers not more than ±0.06 dioptres. The standards refer to this as ‘Optical Class 1’ which in layman terms is a zero-power lens. As per the safety standards lens complying to this are required to have marking ‘1’.
The ISO 16321 standard has pushed the transmittance criterion to 80% and identifies +/- 0.06 dioptre(Category 1) as the optional requirement specific to certain applications such as Welding. For general application the ISO 16321 standard allows optical clarity of =/- 0.12 dioptres which is denoted as Category 2. It is not mandatory to mark a Category 2 but it is required to have category 1 marked on the lens.
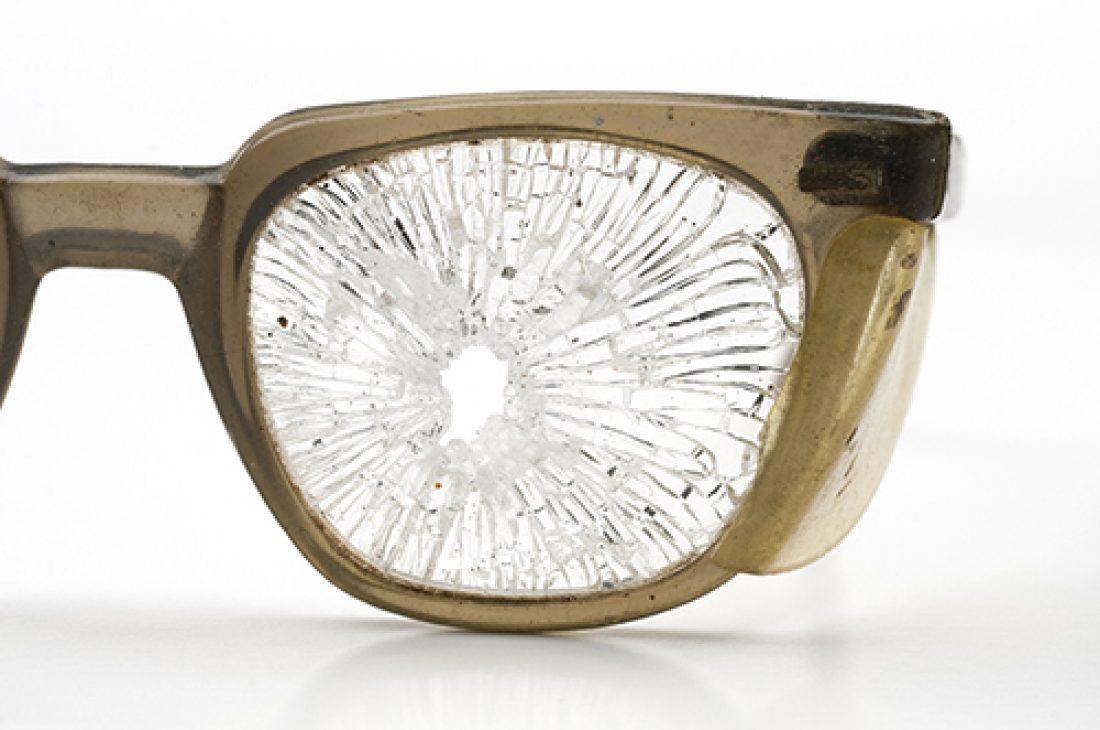
Impact Test/Mechanical Strength
Ability of the safety eyewear to prevent any flying object from getting into our eyes and causing injury would be our next conern and its also a mandatory requirement identified by the safety standards
Most safety standards mandate testing safety ‘spectacles’ against mechanical impact from flying objects at 45m/s which is over 160 km/hr!! One might wonder what’s moving at such breakneck speed at a work area?! The commonly used metal finishing/polishing tools operate at minimum 25 to 30 m/s speed and some grinding wheels need to be operated with 80m/s speed. Any projectile chipping off from the wheel will fly at the same velocity as the grinding or buffing wheel and these are the potential hazards from which the safety eyewear is designed to offer protection to the wearer.
Optical Filters
We have seen that the first safety eyewear was designed for protection against glare and subsequently the need for protection from UV and IR light was also recognized. The information and testing of these array of optical filters is the next mandatory criterion.
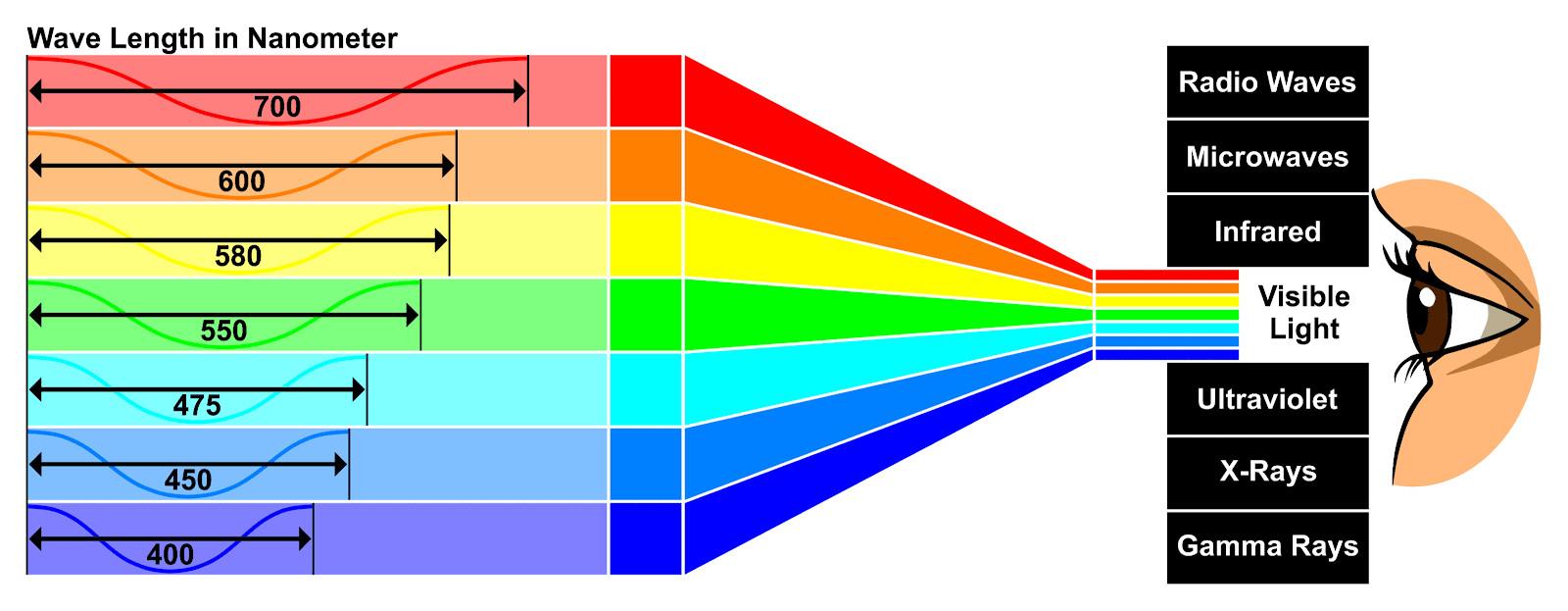
- The UV filter is identified with lens marking ‘2+Shade number’ as per EN standard and ‘U+Shade number’ as per ISO standard
- Infrared filter (for welding or gas cutting exposure) are marked as ‘4+Shade number’ as per EN standard and as per ISO the lens needs to be marked ‘R + shade number’
- For Sun shades the marking is ‘5+shade number’ as per EN and ‘G+shade category’ as per ISO
- The shade number indicates darkness of the lens – higher the shade number darker is the lens. Shade 1.2 typically is a clear lens with over 74% transmittance of visible light spectrum and the darker shades go up to Shade 5 with visible light transmittance between 1.2% to 3.2%
- As per ISO standard a letter L should follow the Optical filter (e.g. UL or GL) to denote compliance to ‘traffic signal color recognition’.
Other mandatory requirements
It is mandatory under both EN and ISO standards to have the manufacturer's identity mark on the lens and the frame. In addition, the number of standards i.e.,166 for EN and 16321 for ISO should also be marked on the frame.
OPTIONAL OR ADDITIONAL MARKINGS
Now lets understand additional or optional requirements. Ironically the most sought after features of scratch resistance and anti-fog performance are considered additional requirements. The standards also recognize other optional requirements like operating performance under extreme temperatures and protection against chemical splash, gas, molten metals or fine dust.
The product needs to have suitable markings if the manufacture is claiming to offer any of these additional features.
Scratch Resistance
An eyewear claiming to offer scratch resistance (surface damage by fine particles) needs to have marking K on the lens under both the standards.
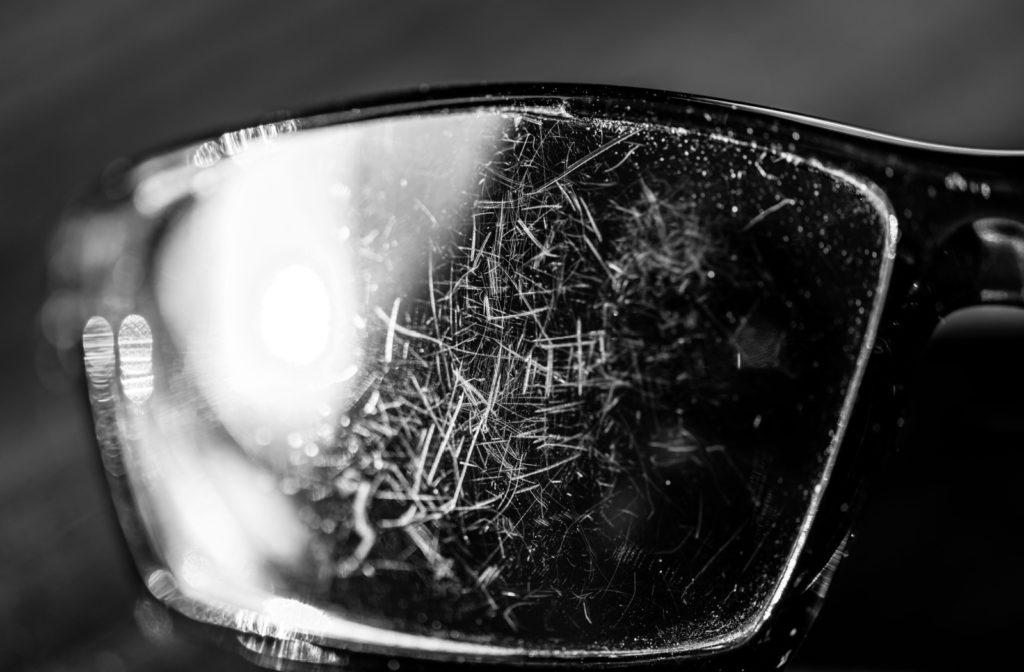
We have seen earlier that because of its mechanical strength Polycarbonate is material of choice for most safety eyewear. However, polycarbonate is soft material that’s easily prone to scratches. For this reason, all polycarbonate lenses are provided with a coating which forms a physical barrier over the polycarbonate surface. The strength and thickness of this coating will determine the degree of the scratch resistance and thus will influence if an eyewear gets worn or not.
An eyewear with K marking ensures a fair degree of scratch resistance and can ensure durability of the product.
Resistance to Fogging
Fogging is second most challenging issues that makes the user remove their eyewear and thus increase their exposure to risk. Many users are required to wear a dust mask along with their safety eyewear and the warm exhalation fog up the lenses. Individuals working in cooler rooms with tightly worn goggles can also experience fogging of lenses.
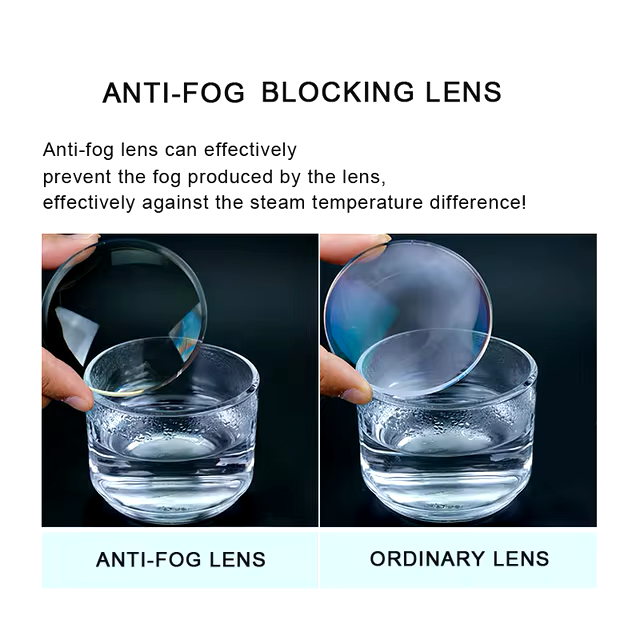
An anti-fog compliance calls for the lenses to remain fog free for a minimum 8 seconds when exposed to an atmosphere above 50 °C.
Both EN and ISO standard use letter N to denote an acceptable resistance to fogging.
Other Optional Compliances
Protection against liquid splash, large dust particles, gas and molten metal is denoted with frame marking 3, 4, 5 and 9 respectively under both the standards.
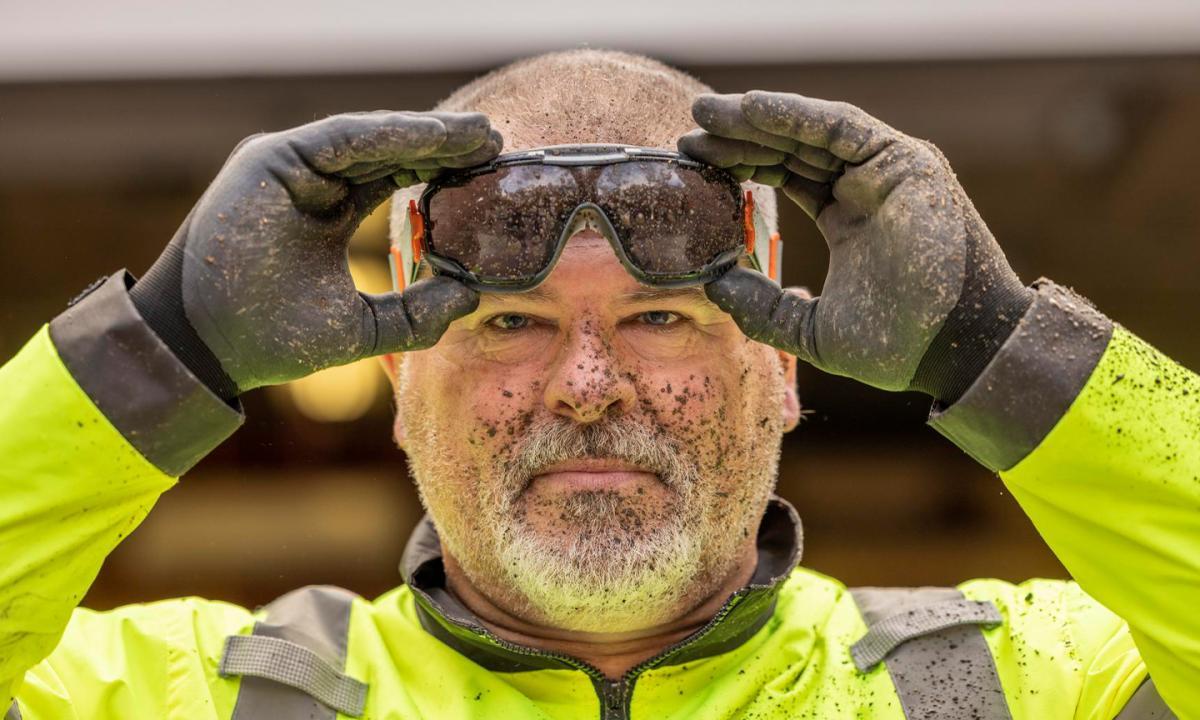
Protection against these hazards might call for some specific product features which are application specific e.g products offering protection from gas or very fine particles will have reduced ventilation compared to products offering protection against large particles
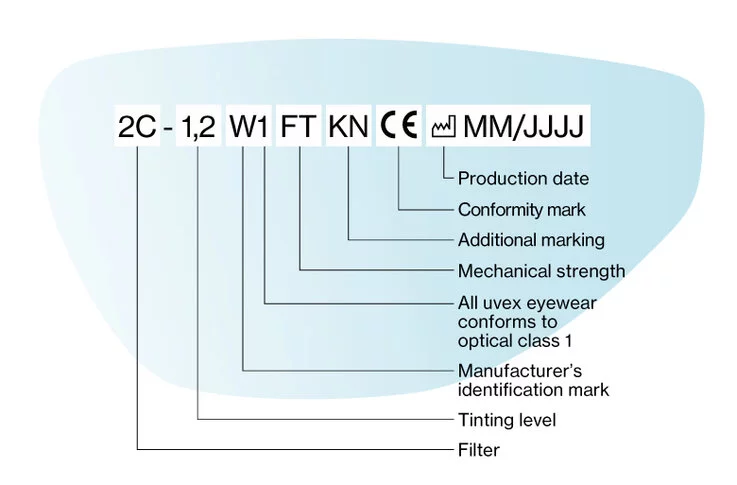
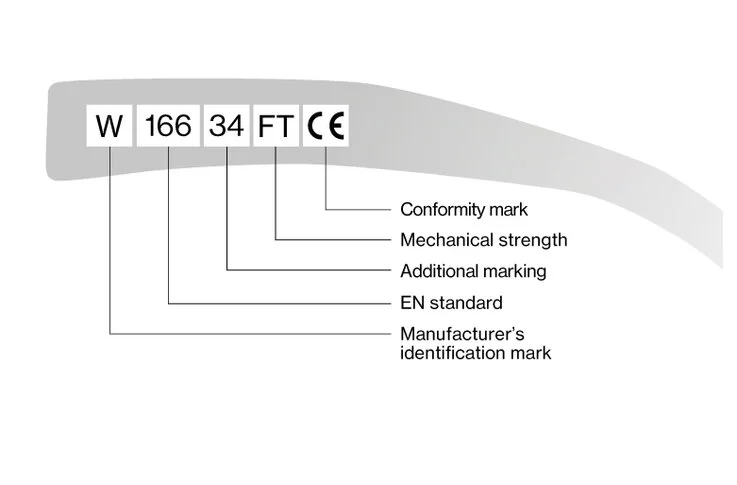
Now let’s circle back to where we originally started - the challenge of defining a bare minimum for a given work environment with defined hazards without compromising the compliance. With the knowledge of product markings the decision makers can easily select an appropriate safety eyewear which will protect the wearer from the hazards at the workplace and will also ensure that it gets worn! e.g Individuals working at a chemical laboratory are required to wear a goggle and typically they are troubled with fogged lenses and hence skip wearing the goggle making them susceptible to risk. For such application the decision parameter should not just be limited to the chemical splash protection (frame marking 3) but the anti-fog performance of the lenses (i.e lenses with marking K) should also be considered while selecting the goggle.
With this information about the expected performance parameters, it is easy to understand why a competitively priced general purpose eyewear without N marking doesn’t get worn. The product that compromises on sufficient scratch resistance will develop scratches quickly and will not have a long life in use thus reducing compliance and increasing risks!
The knowledge of safety standards provides sufficient clarity to the decision makers to map a product to an application thereby eliminating the bare minimum compromise and ensure maximum protection to the wearers.
The Indian standard for Safety Eyewear is now harmonized to ISO 16321. The EN standard will also be migrated to this ISO standard by Nov 2025. As the ISO standard gain worldwise adoption, it will ensure universal minimum standard for safety, offering greater protection and consistency across international markets.